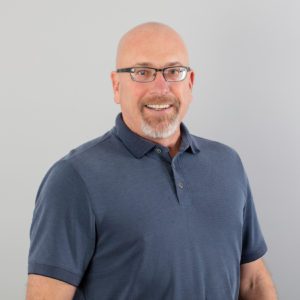
by Jon DadyClient Solutions ManagerIn a collision repair shop, there are always a lot of tasks to be done, but at the heart of it, we need to repair vehicles correctly, efficiently, and on time. When I was running a shop, I found myself spending a ton of time walking back and forth: from my desk to a car back to my desk to the paint bay to the disassembly area to my desk and so on. While it was good for my step count, I knew that for things to run well, I had to make better use of my time, and my team’s time, at the car.The Customer Experience at the CarEvery collision has a story. I need to hear, from the customer, the story of how the vehicle made its way into my shop. What better place to hear that story than at the car during customer drop off?A quick walkaround with the customer provides the opportunity to talk about what damages are related to the accident and what ones aren’t. This can help to avoid the “that wasn’t there” conversation that can happen at the end of the repair.Spending more time with the customer at the car also shows empathy. As they tell the story of the collision, you can begin to tell another story: the story of the repair. Reinforce how the ADAS features worked to reduce the severity of damages and bodily injuries. Educate the customer on what you expect to see through your knowledgeable eyes and what you expect once the vehicle has been disassembled.These “at the car” conversations can build trust through explaining that damage can go beyond what is visible and by being transparent about the repair process.Your Experience at the CarFor estimators, technicians, and production managers, advancements in technology have made it easier than ever to be more productive and spend more time at the car.During the customer drop off, estimators can use a tablet to take photos and write estimates, capturing important information BEFORE walking back to a desk. Writing a full sheet at the car where every clip, bolt and retainer is noted can cut down on supplements and having to wait because an incorrect part was ordered.Gone are the days of not being able to read your own writing (I’m guilty of that!), trying to remember if a spare wheel well was for a donut or full-size spare, or if a side marker lamp was clear or amber. At the car, any information you need is at your fingertips: options, packages, PDC sensors, foldable mirrors, etc.In addition to Estimators, Technicians can check on parts, complete repair phases (which can then automatically update the customer), and upload additional photos like blend photos or polish / de-nib photos from the paint booth at the car. Additionally, repair procedures can be accessed without ever leaving the bay, resulting in a more efficient use of time (not to mention a more accurate repair).For production managers, technology allows for checking on assigned labor, seeing what has been dropped off, and what vehicles may have been forgotten about.All shops get busy, and I’m sure yours is no different. When that happens, it’s easy to go on autopilot and do things the way you always have. But think about how you and your team can spend more time at the car, and the impact that can have on your estimates and on your cycle times. The next time you walk back to your computer, ask yourself "Could I have just done that… at the car?"
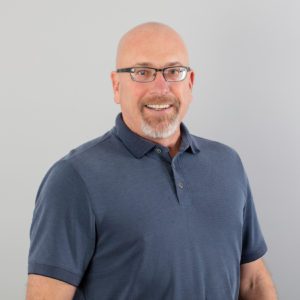
by Jon DadyClient Solutions ManagerIn a collision repair shop, there are always a lot of tasks to be done, but at the heart of it, we need to repair vehicles correctly, efficiently, and on time. When I was running a shop, I found myself spending a ton of time walking back and forth: from my desk to a car back to my desk to the paint bay to the disassembly area to my desk and so on. While it was good for my step count, I knew that for things to run well, I had to make better use of my time, and my team’s time, at the car.The Customer Experience at the CarEvery collision has a story. I need to hear, from the customer, the story of how the vehicle made its way into my shop. What better place to hear that story than at the car during customer drop off?A quick walkaround with the customer provides the opportunity to talk about what damages are related to the accident and what ones aren’t. This can help to avoid the “that wasn’t there” conversation that can happen at the end of the repair.Spending more time with the customer at the car also shows empathy. As they tell the story of the collision, you can begin to tell another story: the story of the repair. Reinforce how the ADAS features worked to reduce the severity of damages and bodily injuries. Educate the customer on what you expect to see through your knowledgeable eyes and what you expect once the vehicle has been disassembled.These “at the car” conversations can build trust through explaining that damage can go beyond what is visible and by being transparent about the repair process.Your Experience at the CarFor estimators, technicians, and production managers, advancements in technology have made it easier than ever to be more productive and spend more time at the car.During the customer drop off, estimators can use a tablet to take photos and write estimates, capturing important information BEFORE walking back to a desk. Writing a full sheet at the car where every clip, bolt and retainer is noted can cut down on supplements and having to wait because an incorrect part was ordered.Gone are the days of not being able to read your own writing (I’m guilty of that!), trying to remember if a spare wheel well was for a donut or full-size spare, or if a side marker lamp was clear or amber. At the car, any information you need is at your fingertips: options, packages, PDC sensors, foldable mirrors, etc.In addition to Estimators, Technicians can check on parts, complete repair phases (which can then automatically update the customer), and upload additional photos like blend photos or polish / de-nib photos from the paint booth at the car. Additionally, repair procedures can be accessed without ever leaving the bay, resulting in a more efficient use of time (not to mention a more accurate repair).For production managers, technology allows for checking on assigned labor, seeing what has been dropped off, and what vehicles may have been forgotten about.All shops get busy, and I’m sure yours is no different. When that happens, it’s easy to go on autopilot and do things the way you always have. But think about how you and your team can spend more time at the car, and the impact that can have on your estimates and on your cycle times. The next time you walk back to your computer, ask yourself "Could I have just done that… at the car?"