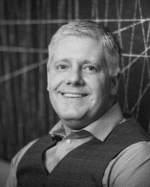
Dan RisleyVP, ASG Market Solutions
I hope that the quality control in your shop is MIA! Yes, you read that correctly; M. I. A. Before you stop reading, you should know I don’t mean that your quality control should be Missing In Action. I’m referring to three other words that should be a part of any business that is focused on repair quality and continuous improvement:
-Measuring
-Improving
-Analyzing
The idea of controls to gauge repair quality isn't new, but processes like scanning and calibrations are becoming more and more commonplace. In fact, the latest Crash Course statistics illustrate a few key points and trends:
- Over 47% of all estimates included a line item for a scan in Q1 2021. This is a 44% increase from just four years ago.
- In 2017, fewer than 1% of estimates had a line item for calibrations. Now, 5% of estimates have calibrations; 10%+ of estimates newer than three years have calibrations.
This trend will likely continue, and even accelerate, as newer model vehicles equipped with more advanced driver assistance systems (ADAS) arrive in showrooms (and then body shops) around the country. Even vehicles that have been on the road for years have complicated systems.So how does “measuring, improving, and analyzing” impact repair quality relative to scanning and calibrations? Well, if you aren’t already implementing an M-I-A approach, your quality may already be suffering the consequences.
Measuring
Measuring the impact of ADAS-equipped vehicles on your shop’s performance is a multifaceted approach. Start with the basics. We already noted that 47% of all estimates had a scan charge, and 5% had a line item for calibration. These percentages will fluctuate based upon vehicle mix and the type of repair, but it’s a starting point. If you’re repairing newer model vehicles, the percentage of scans and calibrations should be higher.Your baseline measurement should go beyond just the percentage of vehicles being scanned and calibrated. To get a full lay of the land, look at how the growth of ADAS-equipped vehicles has impacted your business. Perhaps you're writing more supplements, or there’s an increase in cycle times because you sublet the scanning and calibration to a third party vendor, like your local dealer. Are repairs on vehicles with ADAS returning lower CSI scores than those without? Are those jobs taking longer? These and more should all be part of the initial measurement of your shop's performance.
Improving
Your secret weapon(s) are improvement and investment based on that data – especially in scanning and calibrations. That investment will come in many different forms. Investing time, resources, and money to train and educate your team on improved processes is one that you won’t regret and one your customer will thank you for.Pre-repair scanning during the blueprinting process can help to identify diagnostic trouble codes (DTCs) and ADAS equipment impacted in a collision, meaning fewer supplements. Post-repair scans before the vehicle leaves the shop can drive more positive CSI scores by cutting down the number of vehicles being returned for additional repairs.Improvement could also come through a financial investment to bring scanning and calibrations in-house. This investment often leads to reduced cycle times and increased customer satisfaction.
Analyzing
Once new processes have been put into place, it's time to analyze how it has helped your business. Like we did in the Measurement phase, look at performance through the lens of cycle time and customer satisfaction: have the changes helped to reduce the overall cycle time and/or improved your CSI? It's likely that BOTH will occur once you have committed to the investment in your team and your process.The percentage of new vehicles with at least one ADAS feature is on the rise and will likely hit 100% in the not-too-distant future. Don't be afraid to go M-I-A as the industry evolves. Measure, Improve, and Analyze to stay ahead of the competition.
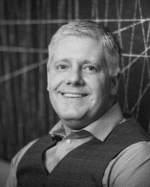
Dan RisleyVP, ASG Market Solutions
I hope that the quality control in your shop is MIA! Yes, you read that correctly; M. I. A. Before you stop reading, you should know I don’t mean that your quality control should be Missing In Action. I’m referring to three other words that should be a part of any business that is focused on repair quality and continuous improvement:
-Measuring
-Improving
-Analyzing
The idea of controls to gauge repair quality isn't new, but processes like scanning and calibrations are becoming more and more commonplace. In fact, the latest Crash Course statistics illustrate a few key points and trends:
- Over 47% of all estimates included a line item for a scan in Q1 2021. This is a 44% increase from just four years ago.
- In 2017, fewer than 1% of estimates had a line item for calibrations. Now, 5% of estimates have calibrations; 10%+ of estimates newer than three years have calibrations.
This trend will likely continue, and even accelerate, as newer model vehicles equipped with more advanced driver assistance systems (ADAS) arrive in showrooms (and then body shops) around the country. Even vehicles that have been on the road for years have complicated systems.So how does “measuring, improving, and analyzing” impact repair quality relative to scanning and calibrations? Well, if you aren’t already implementing an M-I-A approach, your quality may already be suffering the consequences.
Measuring
Measuring the impact of ADAS-equipped vehicles on your shop’s performance is a multifaceted approach. Start with the basics. We already noted that 47% of all estimates had a scan charge, and 5% had a line item for calibration. These percentages will fluctuate based upon vehicle mix and the type of repair, but it’s a starting point. If you’re repairing newer model vehicles, the percentage of scans and calibrations should be higher.Your baseline measurement should go beyond just the percentage of vehicles being scanned and calibrated. To get a full lay of the land, look at how the growth of ADAS-equipped vehicles has impacted your business. Perhaps you're writing more supplements, or there’s an increase in cycle times because you sublet the scanning and calibration to a third party vendor, like your local dealer. Are repairs on vehicles with ADAS returning lower CSI scores than those without? Are those jobs taking longer? These and more should all be part of the initial measurement of your shop's performance.
Improving
Your secret weapon(s) are improvement and investment based on that data – especially in scanning and calibrations. That investment will come in many different forms. Investing time, resources, and money to train and educate your team on improved processes is one that you won’t regret and one your customer will thank you for.Pre-repair scanning during the blueprinting process can help to identify diagnostic trouble codes (DTCs) and ADAS equipment impacted in a collision, meaning fewer supplements. Post-repair scans before the vehicle leaves the shop can drive more positive CSI scores by cutting down the number of vehicles being returned for additional repairs.Improvement could also come through a financial investment to bring scanning and calibrations in-house. This investment often leads to reduced cycle times and increased customer satisfaction.
Analyzing
Once new processes have been put into place, it's time to analyze how it has helped your business. Like we did in the Measurement phase, look at performance through the lens of cycle time and customer satisfaction: have the changes helped to reduce the overall cycle time and/or improved your CSI? It's likely that BOTH will occur once you have committed to the investment in your team and your process.The percentage of new vehicles with at least one ADAS feature is on the rise and will likely hit 100% in the not-too-distant future. Don't be afraid to go M-I-A as the industry evolves. Measure, Improve, and Analyze to stay ahead of the competition.