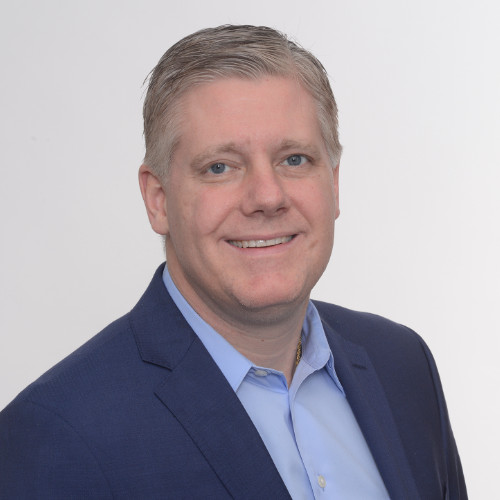
By Dan Risley, Vice President of Repair Quality and Market Development
“We scan every car every time!”
“Yes, scanning is part of our standard operating procedure!”
“ We always perform a pre-scan prior to disassembly and a post-scan prior to delivery.”
When I ask if a shop scans every vehicle, I typically see these unwavering answers. But when I ask the follow-up question, “how do you know all scans were performed?”, there’s often a lot less certainty. Our 2024 Q1 Crash Course report data shows that almost one out of every three 2023 model year vehicles had no scan reported in 2023. Considering ADAS systems are now standard, that stat is incredibly worrisome.
Here are some of the most commonly used ways that shops track scans. Any of them sound familiar?
The Post-It Note
Whenever I need to remember something, I also reach for a handy sticky note. But my notes don’t really remind me of much – other than I have a lot of things to remember. Paper notes on desktops or files don’t really give any assurance scans happened.
The Best Memory in the West
While I love the saying “I just remember not to forget,” it should also come as no surprise that humans forget even the things they try their hardest to remember. If you just know scans are completed, I respect your efforts, but I’d want some hard and true documentation.
The Whiteboard
The issue I have with this is that when I ask if it’s up to date, I’m often told “I don’t know when it was last updated,” or, they can’t find the dry erase pens, or the board has been wiped and written on so many times that the information is unreadable.
The Spreadsheet
Unfortunately, this method also has similar pitfalls – it doesn’t get updated in a timely manner, one person “owns” the spreadsheet they need to remember not to forget to update, or, like me, they may type too quickly and have a string of unintentional errors.
The Digital Solution
A digital, trackable, verifiable solution is my suggestion for shops. After all, it’s not difficult to imagine an estimator inadvertently leaving a scan off an estimate or a busy technician forgetting to perform a post-scan on a crazy Friday afternoon.
Some of the best operators in the industry are averaging less than two scans per repair order despite having SOP’s requiring a pre- and post-scan on every vehicle. As more vehicles are equipped with at least one advanced driver assistance system (ADAS) feature, scanning and calibration percentages will likely continue to increase. Without a tool to manage the process, the challenges you are experiencing today will only compound in the future.
CCC Diagnostics Workflow provides a dashboard view of every vehicle in production (without the use of a dry erase board, taxing your memory, or phoning a friend).
From one digital source of truth, you can know:
- Which repair orders need a pre- or post-scan to be performed.
- Benefit: More efficiently manage production and reduce unnecessary delays.
- Which repair orders are missing a line on the estimate for a pre- or post-scan.
- Benefit: Reduce missed sales opportunities and ensure SOPs are followed.
- Which repair orders have a completed pre- or post-scan but have not been added to the estimate.
- Benefit: Improved profit margins. Reduce situations when an expense is incurred (scan performed) but there is no sale (line on estimate).
Learn more at cccis.com/diagnostics.
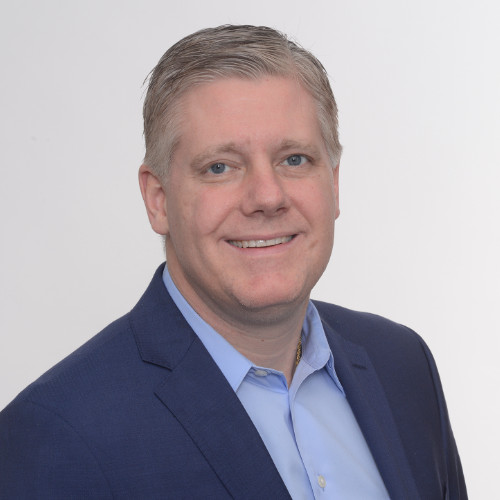
By Dan Risley, Vice President of Repair Quality and Market Development
“We scan every car every time!”
“Yes, scanning is part of our standard operating procedure!”
“ We always perform a pre-scan prior to disassembly and a post-scan prior to delivery.”
When I ask if a shop scans every vehicle, I typically see these unwavering answers. But when I ask the follow-up question, “how do you know all scans were performed?”, there’s often a lot less certainty. Our 2024 Q1 Crash Course report data shows that almost one out of every three 2023 model year vehicles had no scan reported in 2023. Considering ADAS systems are now standard, that stat is incredibly worrisome.
Here are some of the most commonly used ways that shops track scans. Any of them sound familiar?
The Post-It Note
Whenever I need to remember something, I also reach for a handy sticky note. But my notes don’t really remind me of much – other than I have a lot of things to remember. Paper notes on desktops or files don’t really give any assurance scans happened.
The Best Memory in the West
While I love the saying “I just remember not to forget,” it should also come as no surprise that humans forget even the things they try their hardest to remember. If you just know scans are completed, I respect your efforts, but I’d want some hard and true documentation.
The Whiteboard
The issue I have with this is that when I ask if it’s up to date, I’m often told “I don’t know when it was last updated,” or, they can’t find the dry erase pens, or the board has been wiped and written on so many times that the information is unreadable.
The Spreadsheet
Unfortunately, this method also has similar pitfalls – it doesn’t get updated in a timely manner, one person “owns” the spreadsheet they need to remember not to forget to update, or, like me, they may type too quickly and have a string of unintentional errors.
The Digital Solution
A digital, trackable, verifiable solution is my suggestion for shops. After all, it’s not difficult to imagine an estimator inadvertently leaving a scan off an estimate or a busy technician forgetting to perform a post-scan on a crazy Friday afternoon.
Some of the best operators in the industry are averaging less than two scans per repair order despite having SOP’s requiring a pre- and post-scan on every vehicle. As more vehicles are equipped with at least one advanced driver assistance system (ADAS) feature, scanning and calibration percentages will likely continue to increase. Without a tool to manage the process, the challenges you are experiencing today will only compound in the future.
CCC Diagnostics Workflow provides a dashboard view of every vehicle in production (without the use of a dry erase board, taxing your memory, or phoning a friend).
From one digital source of truth, you can know:
- Which repair orders need a pre- or post-scan to be performed.
- Benefit: More efficiently manage production and reduce unnecessary delays.
- Which repair orders are missing a line on the estimate for a pre- or post-scan.
- Benefit: Reduce missed sales opportunities and ensure SOPs are followed.
- Which repair orders have a completed pre- or post-scan but have not been added to the estimate.
- Benefit: Improved profit margins. Reduce situations when an expense is incurred (scan performed) but there is no sale (line on estimate).
Learn more at cccis.com/diagnostics.