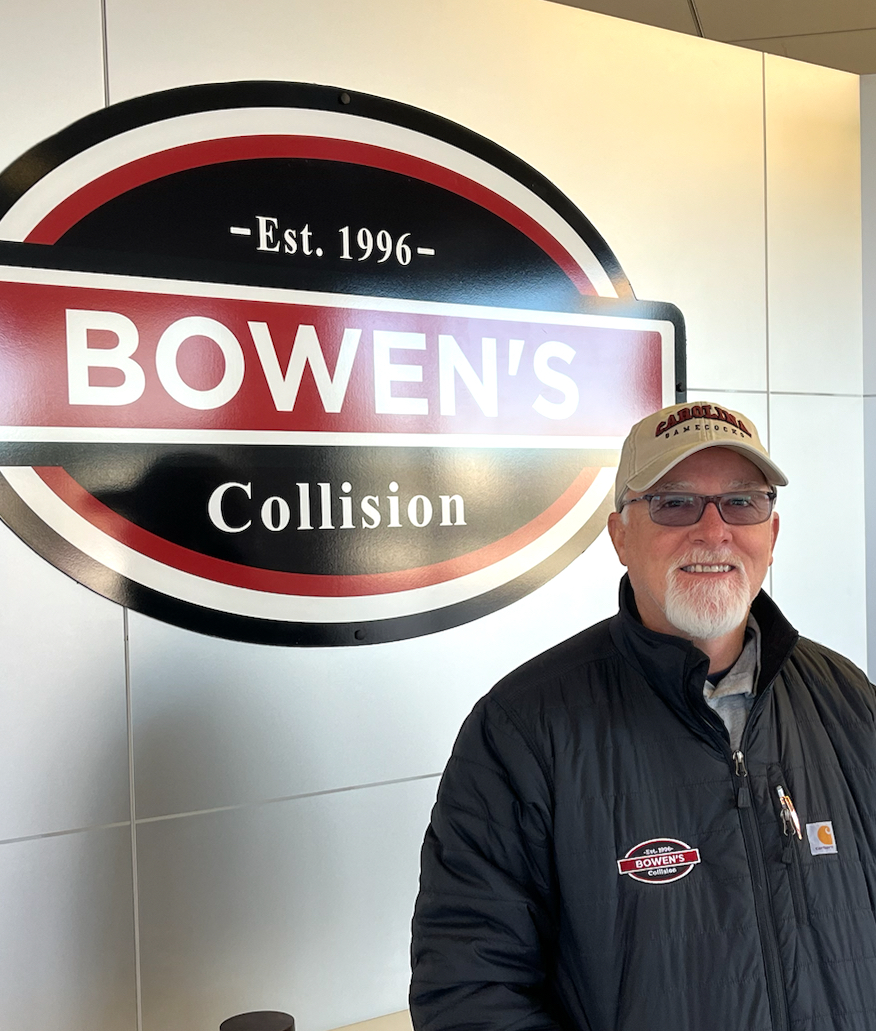
For 27 years, Bowen's Collision has been a pillar of the Columbia, South Carolina community, but it was only in the last two years that the family-owned and operated business experienced impressive growth, adding two new locations, with plans to open more in the next few years.
General Manager Scott Austin attributes Bowen's Collision's success to their world-class customer service and top-quality repairs.
Putting customers first and delivering high-caliber repairs wouldn't be possible without consistent performance, which is why Austin focused on developing more standardized routines and processes for his technicians to streamline things like diagnostic scans, which he believes gives Bowen's Collision a competitive edge.
In fact, the decision to scan every vehicle that comes into the shop was a "no-brainer," according to Austin, because the benefits of doing so far outweigh the drawbacks. He said most manufacturers no longer recommend scans –– they require them, yet not every shop does them consistently.
"Scans cover all the bases," says Austin. "Pre-repair scans help us find out where the initial problems are and eliminate others right away. Documentation beats conversation and having all the information up front helps us know what we’re getting into and be prepared to have a discussion if we have to. It's good for our customers and it's great for our shops."
Austin says the benefits of knowing more about vehicle damage earlier in the repair process can help save everyone time, money, and resources, which leads to happier customers. It's also increased revenue and profitability for his shop, he said. The cost of a brand-new scanner quickly pays for itself because the shop can bill carriers or self-paying customers foreach scan, and the scans aren't time-consuming to perform.
The problem shops often have with integrating diagnostics into their repair processes is "remembering not to forget" to scan or calibrate, sometimes even resorting to sticky notes to remind them of these critical tasks.
Austin says that's why he uses CCC® Diagnostics Workflow, because it helps his team integrate diagnostics into every single repair plan and keep track of every scan all in one place. The result? A diagnostics process that comes naturally to his technicians. They no longer need reminders, and they don't even have to think about it –– it's simply a required operation for every vehicle, every time.
"You've got to make sure you do it, because it's the times you don't that you get whistle bit," Austin says. "We're all about helping people –– that's truly our mission, and if we can make a customer feel better about their repair knowing we did everything we could to diagnose the problem, well, then, we're practicing what we preach."
To learn more about CCC Diagnostics Workflow, visit cccis.com/diagnostics
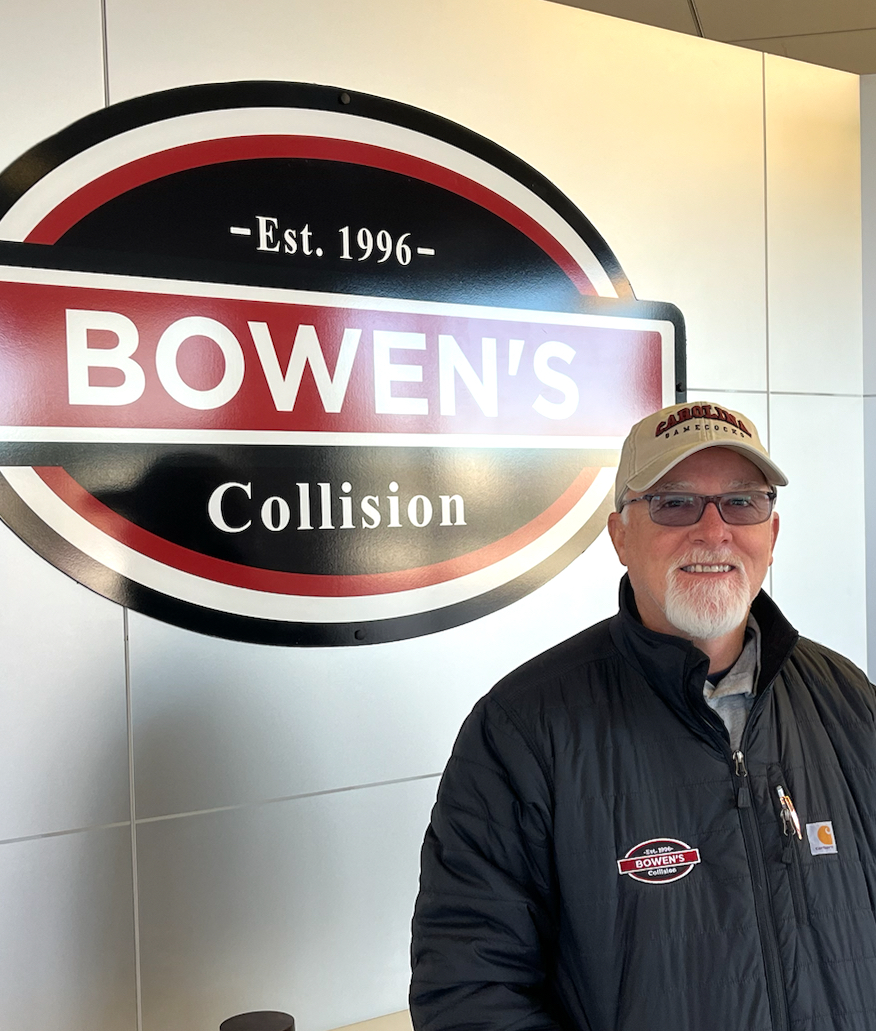
For 27 years, Bowen's Collision has been a pillar of the Columbia, South Carolina community, but it was only in the last two years that the family-owned and operated business experienced impressive growth, adding two new locations, with plans to open more in the next few years.
General Manager Scott Austin attributes Bowen's Collision's success to their world-class customer service and top-quality repairs.
Putting customers first and delivering high-caliber repairs wouldn't be possible without consistent performance, which is why Austin focused on developing more standardized routines and processes for his technicians to streamline things like diagnostic scans, which he believes gives Bowen's Collision a competitive edge.
In fact, the decision to scan every vehicle that comes into the shop was a "no-brainer," according to Austin, because the benefits of doing so far outweigh the drawbacks. He said most manufacturers no longer recommend scans –– they require them, yet not every shop does them consistently.
"Scans cover all the bases," says Austin. "Pre-repair scans help us find out where the initial problems are and eliminate others right away. Documentation beats conversation and having all the information up front helps us know what we’re getting into and be prepared to have a discussion if we have to. It's good for our customers and it's great for our shops."
Austin says the benefits of knowing more about vehicle damage earlier in the repair process can help save everyone time, money, and resources, which leads to happier customers. It's also increased revenue and profitability for his shop, he said. The cost of a brand-new scanner quickly pays for itself because the shop can bill carriers or self-paying customers foreach scan, and the scans aren't time-consuming to perform.
The problem shops often have with integrating diagnostics into their repair processes is "remembering not to forget" to scan or calibrate, sometimes even resorting to sticky notes to remind them of these critical tasks.
Austin says that's why he uses CCC® Diagnostics Workflow, because it helps his team integrate diagnostics into every single repair plan and keep track of every scan all in one place. The result? A diagnostics process that comes naturally to his technicians. They no longer need reminders, and they don't even have to think about it –– it's simply a required operation for every vehicle, every time.
"You've got to make sure you do it, because it's the times you don't that you get whistle bit," Austin says. "We're all about helping people –– that's truly our mission, and if we can make a customer feel better about their repair knowing we did everything we could to diagnose the problem, well, then, we're practicing what we preach."
To learn more about CCC Diagnostics Workflow, visit cccis.com/diagnostics