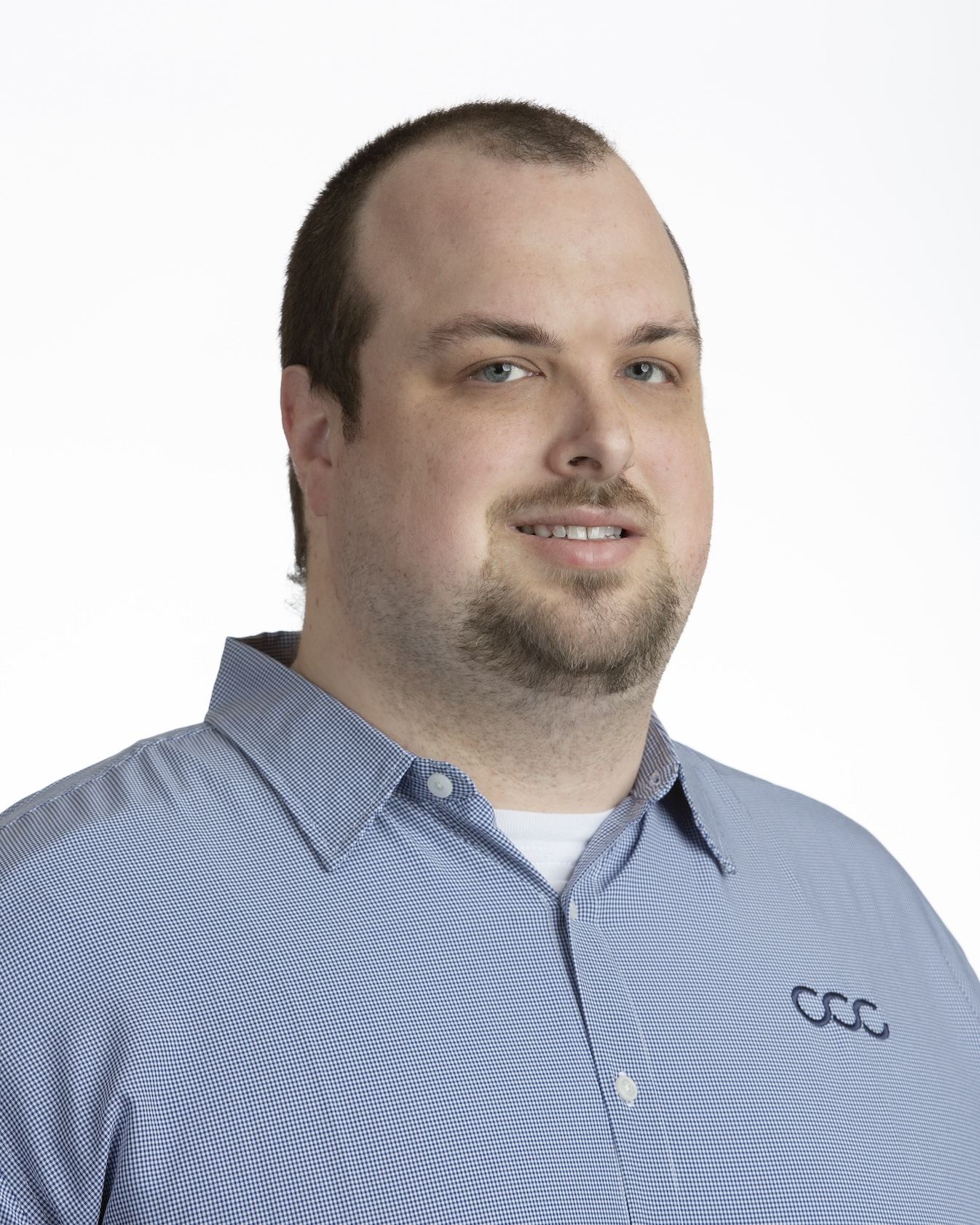
By: Blake Levesque, Client Solutions Advisor
In today's fast-paced, ever-changing automotive repair industry, keeping employees on the same page is more challenging than ever – and a one size fits all approach to production management just won't cut it.
In my role as a Client Solutions Advisor, I spend my days in shops across my home state of Wisconsin. I have shops that service major cities and small towns, but no two shops are alike.
One of my favorite ways to help a shop customize their CCC tools is to show them a new feature for our shop management customers within cccone.com – Digital Production Board. In one place, every area of the shop can keep in lockstep from the customer service representative to the estimators, to the technicians, all who have differing needs on what information is important to doing their job, without having to look very far.
Still not sure if this new, free tool is right for you? Here's what I've found from working in shops like yours:
Your Shop, Your Rules
Every shop has their own flavor of how they track production. Maybe you print out a production schedule and talk through it each morning, or you have a faded whiteboard that may or may not have this week’s vehicles. Or maybe you could manage your production schedule online…
That's the beauty of the digital production board. From one place online, you can customize boards to fit your needs – both for the shop as a whole and individually. A painter may only be concerned with the paint hours on a job, while a production manager is concerned with not assigning labor until all the parts are in. Your production manager can have a 10,000 ft view of the shop, while each technician can have their own board to track just their jobs.
The flexibility allows the boards to scale with the repair facility’s growth or adapt on the fly to changing business needs.
For the Visual Learner
When I first started spending time in shops, one of the first things I noticed was the noise – and not just how loud a shop can be, but the mental load each person has trying to keep all their tasks straight. The activity "noise" alone can be overwhelming: a tow truck dropping off a car, a customer dropping in for an estimate, a parts delivery, and a sublet vendor can all be buzzing around at the same time.
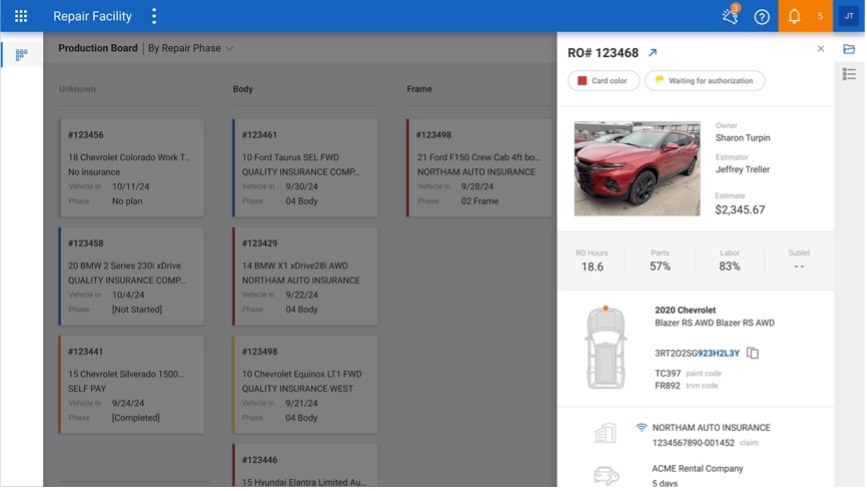
You need something that can cut through the noise and help your team focus on their specific tasks at hand. This is the power of the production board. One place that visually can represent the production schedule of your shop that updates easily and helps your team visualize the flow of vehicles.
The beauty of this visual board is that it also can be used in lots of places. A technician may have it on their workstation to see what to work on next, the production manager may have it on a recently-dusted-off tablet to update production phases in real-time, and the whole shop can see what's going on from a board on a shared big screen.
One source of truth that's easy for anyone to understand can help your shop work smoothly as a team.
Working All Together
The benefit of working with someone like CCC is that all the tools work together in harmony. The same can be said for production boards. When you make an update to a vehicle by dragging and dropping into a new phase, your production schedule will also update.
That connected, harmonious flow extends into all your shop, too. For example, consider your customer service representatives. If a customer calls asks about vehicle status, a well-orchestrated game of telephone usually occurs: the rep asks the estimator, who then asks technician, who then lets you know the detailer is getting the car ready for pickup.
Rather than this complicated update process, a well-connected team could have cut out multiple middlemen to find the answer to "is my car ready?" A customer service team member could look at the board and see where a car is on their own and update the customer while they were still on the phone. No putting them on hold, no chasing down information.
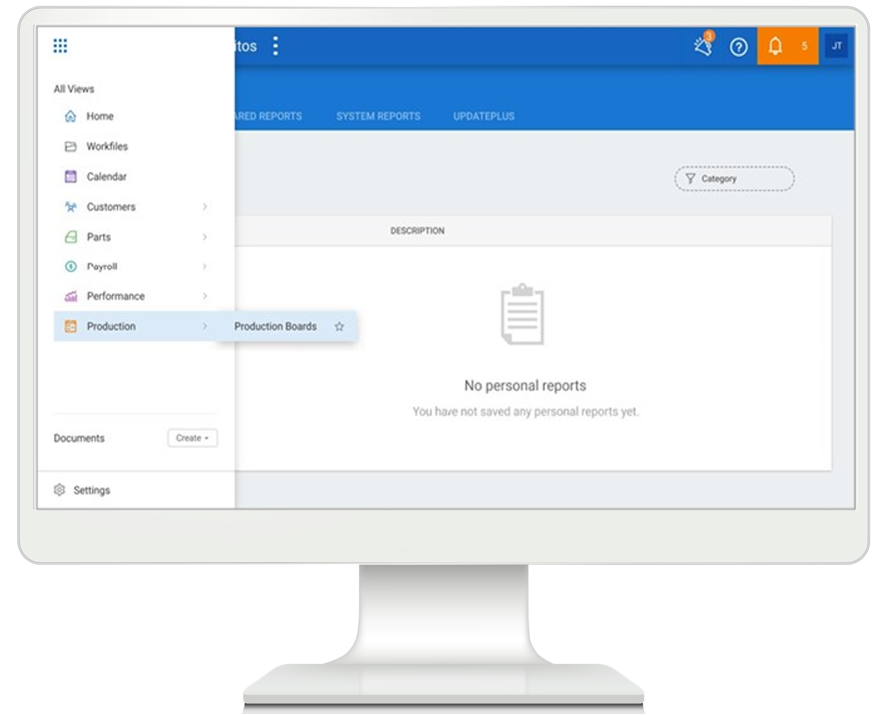
As I said before, taking advantage of this free tool is simple if you already have our Repair Workflow shop management tools – just log in to cccone.com, click the left-hand navigation to open "Production Board," and follow the prompts.
That's it. Simple steps to take advantage of a tool that can transform your production meetings, reducing guesswork and outdated information. From one place, show how the pieces of your shop’s production puzzle fit together so your team can keep plugging along, effectively and all together.
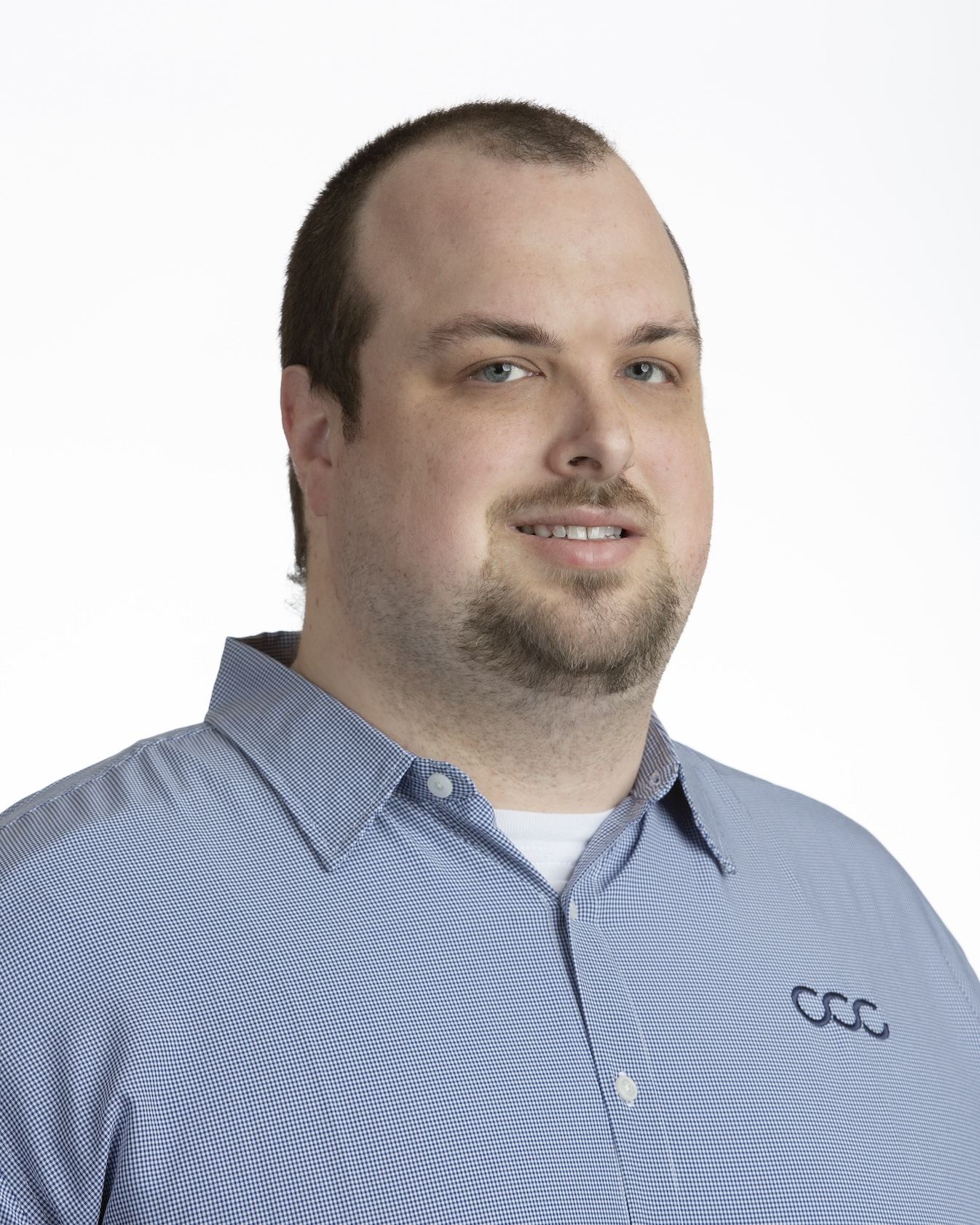
By: Blake Levesque, Client Solutions Advisor
In today's fast-paced, ever-changing automotive repair industry, keeping employees on the same page is more challenging than ever – and a one size fits all approach to production management just won't cut it.
In my role as a Client Solutions Advisor, I spend my days in shops across my home state of Wisconsin. I have shops that service major cities and small towns, but no two shops are alike.
One of my favorite ways to help a shop customize their CCC tools is to show them a new feature for our shop management customers within cccone.com – Digital Production Board. In one place, every area of the shop can keep in lockstep from the customer service representative to the estimators, to the technicians, all who have differing needs on what information is important to doing their job, without having to look very far.
Still not sure if this new, free tool is right for you? Here's what I've found from working in shops like yours:
Your Shop, Your Rules
Every shop has their own flavor of how they track production. Maybe you print out a production schedule and talk through it each morning, or you have a faded whiteboard that may or may not have this week’s vehicles. Or maybe you could manage your production schedule online…
That's the beauty of the digital production board. From one place online, you can customize boards to fit your needs – both for the shop as a whole and individually. A painter may only be concerned with the paint hours on a job, while a production manager is concerned with not assigning labor until all the parts are in. Your production manager can have a 10,000 ft view of the shop, while each technician can have their own board to track just their jobs.
The flexibility allows the boards to scale with the repair facility’s growth or adapt on the fly to changing business needs.
For the Visual Learner
When I first started spending time in shops, one of the first things I noticed was the noise – and not just how loud a shop can be, but the mental load each person has trying to keep all their tasks straight. The activity "noise" alone can be overwhelming: a tow truck dropping off a car, a customer dropping in for an estimate, a parts delivery, and a sublet vendor can all be buzzing around at the same time.
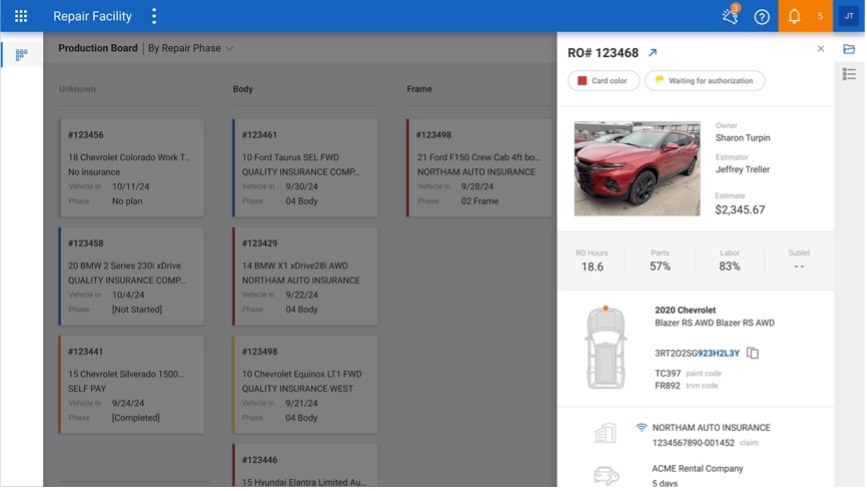
You need something that can cut through the noise and help your team focus on their specific tasks at hand. This is the power of the production board. One place that visually can represent the production schedule of your shop that updates easily and helps your team visualize the flow of vehicles.
The beauty of this visual board is that it also can be used in lots of places. A technician may have it on their workstation to see what to work on next, the production manager may have it on a recently-dusted-off tablet to update production phases in real-time, and the whole shop can see what's going on from a board on a shared big screen.
One source of truth that's easy for anyone to understand can help your shop work smoothly as a team.
Working All Together
The benefit of working with someone like CCC is that all the tools work together in harmony. The same can be said for production boards. When you make an update to a vehicle by dragging and dropping into a new phase, your production schedule will also update.
That connected, harmonious flow extends into all your shop, too. For example, consider your customer service representatives. If a customer calls asks about vehicle status, a well-orchestrated game of telephone usually occurs: the rep asks the estimator, who then asks technician, who then lets you know the detailer is getting the car ready for pickup.
Rather than this complicated update process, a well-connected team could have cut out multiple middlemen to find the answer to "is my car ready?" A customer service team member could look at the board and see where a car is on their own and update the customer while they were still on the phone. No putting them on hold, no chasing down information.
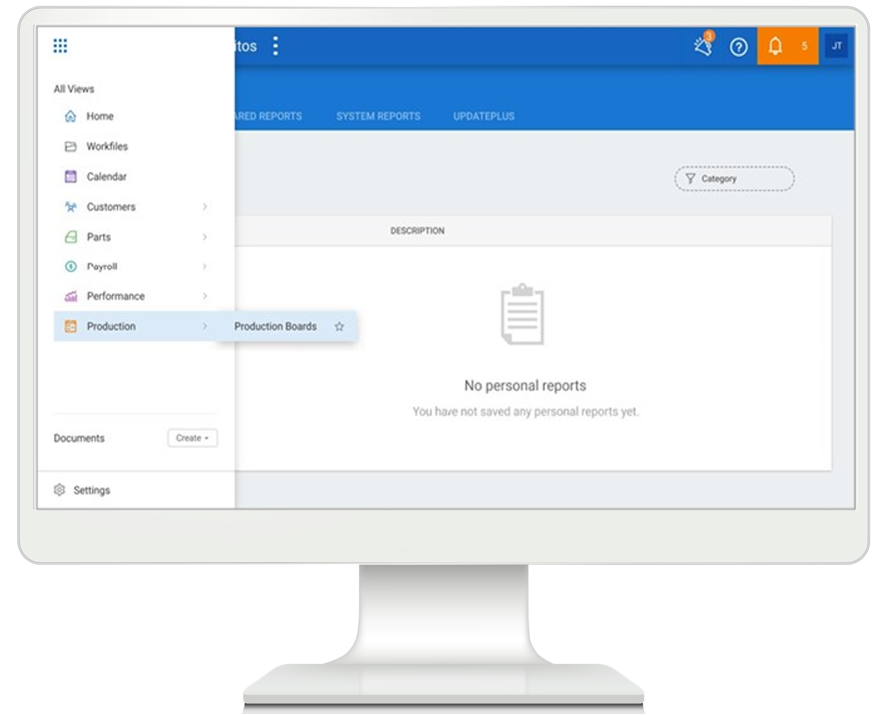
As I said before, taking advantage of this free tool is simple if you already have our Repair Workflow shop management tools – just log in to cccone.com, click the left-hand navigation to open "Production Board," and follow the prompts.
That's it. Simple steps to take advantage of a tool that can transform your production meetings, reducing guesswork and outdated information. From one place, show how the pieces of your shop’s production puzzle fit together so your team can keep plugging along, effectively and all together.