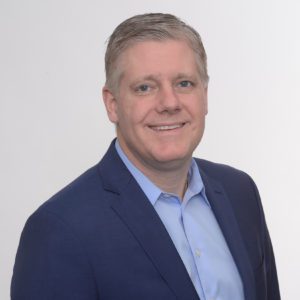
by Dan RisleyVice President, ASG Market SolutionsI’ve written in the past about the importance of diagnostics but I want to address a specific phrase I hear over and over again in shops: “Oh, it’s just a bumper job.”It’s a bit of a running joke that bumpers have become the proxy for simple repairs, or ones that likely won’t require a scan or, even more eye-popping, "a calibration." But even a minor impact or scratch to the front bumper cover could result in a repair that goes far beyond the simplicity associated with the of a traditional bumper repair.
“Simple” Bumper Job No More
According to the National Highway Traffic Safety Administration (NHTSA), more than half of all crashes in 2019 involved an initial front impact. And it used to be that shops had only a few options relative to a damaged front cover: repair, refinish or replace. The “just a bumper job” phrase was close to the mark. It didn't require special tools to complete a safe and proper repair. Depending upon the extent of the damage, it really could be a relatively simple repair.However, with today's newer model vehicles, the narrative is different and simple is no longer simple. In fact, some car manufacturers require a scan and calibration to be completed when the front bumper cover is simply removed and reinstalled, regardless of the amount of damage or the area impacted.A 2021 model sedan has a 95% likelihood of having advanced emergency braking (AEB) systems, including a sensor that is most likely located behind the front bumper cover. By September 1, 2022, AEB will be the standard on all new makes and models. A “simple bumper job” now may require specialized scanning and calibration equipment and a technician trained to scan and calibrate the advanced driver assistance systems.
What to do for no-longer-simple Bumper Jobs
With these changes, diagnostic scanning and system calibrations have never been more important. I personally believe that every repair should start and end with a diagnostic scan.These scans are critically important – not just to help identify ADAS items that may not have triggered a dashboard indicator, but also to protect your customers. When a vehicle arrives at your shop and the bumper is impacted, I encourage you to think twice before making the assumption that "it’s just a bumper job" and a scan is not warranted.
An unexpected benefit - higher satisfaction
CCC’s 2022 Crash Course covers trends in scanning and provides some interesting data about how diagnostics is linked to not just repair accuracy, but also CSI:
- The percent of estimates with a scan grew from 5% (2017) to 48% (2021).
- Over 35% of repair costs are now in supplements. Often, more supplements means a longer cycle time. Accounting for diagnostic scans in the initial estimate can help reduce the number and size of supplements, thereby reducing your cycle time and unnecessary delays.
- Cycle time and customer satisfaction are directly linked. The highest Net Promoter Scores (NPS) typically occur when the time from FNOL to estimate creation was the lowest. The same holds true during the repair process - the sooner customers get their vehicles back, the happier they are.
Taking the time to explain diagnostic scan results and how you addressed them to your customers can also create a higher degree of trust and understanding.OEMs have taken steps to ensure a vehicle is repaired properly by endorsing pre- and post-repair scans. Twenty-eight different brands have issued position statements advising that scans are an important part of the repair process. Some OEMs, like Volvo, have made these scans a requirement on all models made after 1996 if they’re involved in any collision.So while we may still comment about the humble bumper job, technology, safety, and regulations now mean that “just a bumper job” is anything but simple.
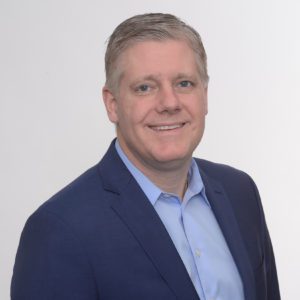
by Dan RisleyVice President, ASG Market SolutionsI’ve written in the past about the importance of diagnostics but I want to address a specific phrase I hear over and over again in shops: “Oh, it’s just a bumper job.”It’s a bit of a running joke that bumpers have become the proxy for simple repairs, or ones that likely won’t require a scan or, even more eye-popping, "a calibration." But even a minor impact or scratch to the front bumper cover could result in a repair that goes far beyond the simplicity associated with the of a traditional bumper repair.
“Simple” Bumper Job No More
According to the National Highway Traffic Safety Administration (NHTSA), more than half of all crashes in 2019 involved an initial front impact. And it used to be that shops had only a few options relative to a damaged front cover: repair, refinish or replace. The “just a bumper job” phrase was close to the mark. It didn't require special tools to complete a safe and proper repair. Depending upon the extent of the damage, it really could be a relatively simple repair.However, with today's newer model vehicles, the narrative is different and simple is no longer simple. In fact, some car manufacturers require a scan and calibration to be completed when the front bumper cover is simply removed and reinstalled, regardless of the amount of damage or the area impacted.A 2021 model sedan has a 95% likelihood of having advanced emergency braking (AEB) systems, including a sensor that is most likely located behind the front bumper cover. By September 1, 2022, AEB will be the standard on all new makes and models. A “simple bumper job” now may require specialized scanning and calibration equipment and a technician trained to scan and calibrate the advanced driver assistance systems.
What to do for no-longer-simple Bumper Jobs
With these changes, diagnostic scanning and system calibrations have never been more important. I personally believe that every repair should start and end with a diagnostic scan.These scans are critically important – not just to help identify ADAS items that may not have triggered a dashboard indicator, but also to protect your customers. When a vehicle arrives at your shop and the bumper is impacted, I encourage you to think twice before making the assumption that "it’s just a bumper job" and a scan is not warranted.
An unexpected benefit - higher satisfaction
CCC’s 2022 Crash Course covers trends in scanning and provides some interesting data about how diagnostics is linked to not just repair accuracy, but also CSI:
- The percent of estimates with a scan grew from 5% (2017) to 48% (2021).
- Over 35% of repair costs are now in supplements. Often, more supplements means a longer cycle time. Accounting for diagnostic scans in the initial estimate can help reduce the number and size of supplements, thereby reducing your cycle time and unnecessary delays.
- Cycle time and customer satisfaction are directly linked. The highest Net Promoter Scores (NPS) typically occur when the time from FNOL to estimate creation was the lowest. The same holds true during the repair process - the sooner customers get their vehicles back, the happier they are.
Taking the time to explain diagnostic scan results and how you addressed them to your customers can also create a higher degree of trust and understanding.OEMs have taken steps to ensure a vehicle is repaired properly by endorsing pre- and post-repair scans. Twenty-eight different brands have issued position statements advising that scans are an important part of the repair process. Some OEMs, like Volvo, have made these scans a requirement on all models made after 1996 if they’re involved in any collision.So while we may still comment about the humble bumper job, technology, safety, and regulations now mean that “just a bumper job” is anything but simple.